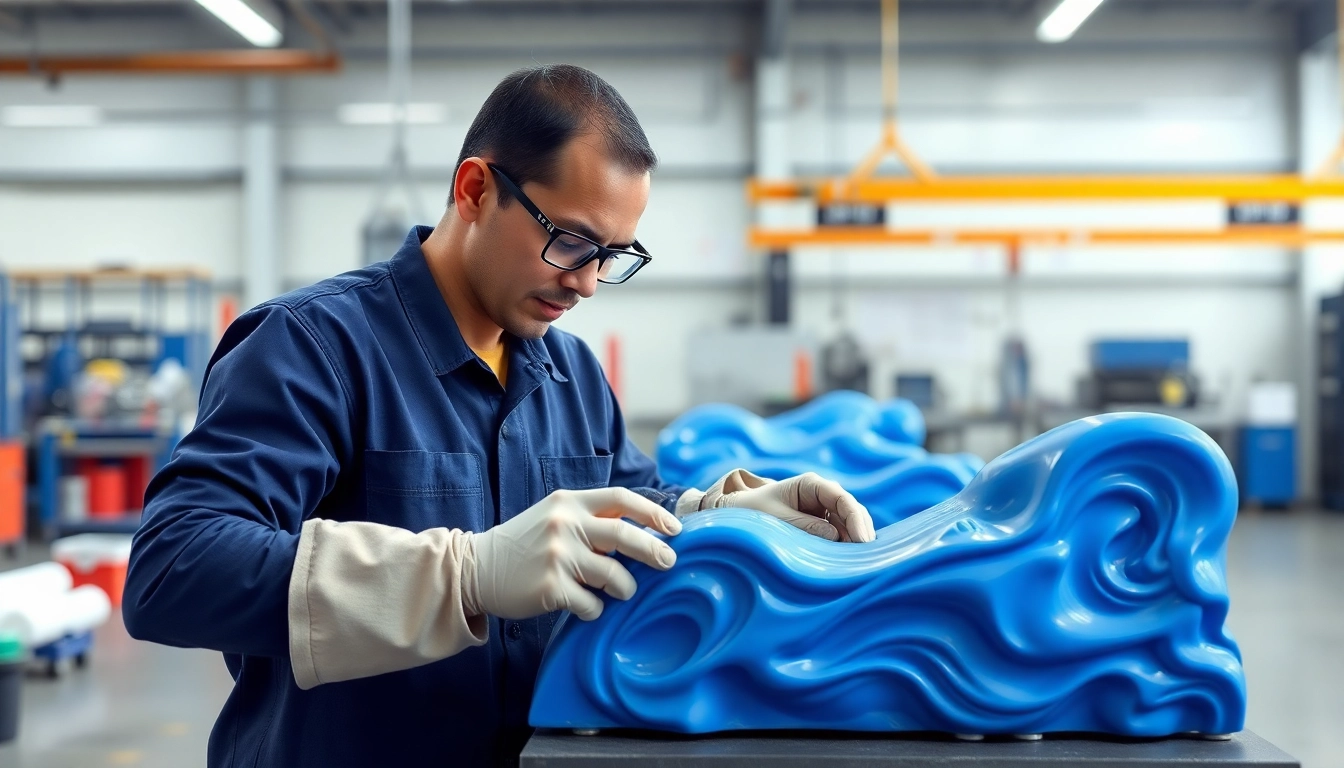
Introduction to Blow Molding Technology
Blow molding is a widely used manufacturing process that leverages the properties of plastics to create hollow objects. As a critical aspect of modern manufacturing, blow molding stands out for its versatility, efficiency, and capability to produce complex shapes. The significance of this technology has led to the rise of numerous blow molding machine manufacturers who specialize in designing and producing machines tailored to various industry needs. This article dives into the fundamental principles of blow molding, how to choose a reliable manufacturer, innovations within the technology, cost considerations, and future trends shaping the industry.
The Basics of Blow Molding
Blow molding is a process that involves heating plastic until it becomes pliable, followed by forming it into a desired shape using air pressure. The fundamental steps include:
- Material Preparation: Plastic resins, typically in granulate form, are fed into a hopper of the blow molding machine and then heated until molten.
- Parison Creation: The heated plastic is extruded into a hollow tube known as a parison.
- Mold Closure: The parison is captured by a two-part mold, which is then closed.
- Air Injection: Air is injected into the mold to expand the parison against the mold walls, forming the final product.
- Cooling and Ejection: The mold is cooled, usually with water, to solidify the plastic, after which the finished part is ejected from the mold.
Types of Blow Molding Processes
Blow molding can be categorized into three primary processes, each with its unique applications and advantages:
- Extrusion Blow Molding (EBM): This is the most common technique used for manufacturing hollow plastic parts, such as bottles and containers. EBM utilizes a continuous extrusion process and is particularly well-suited for high-volume production.
- Injection Blow Molding (IBM): Involves forming a preform using injection molding and then transferring it to a blow mold where air is used to shape it. This method provides better precision and is often used for smaller, intricate items.
- Stretch Blow Molding: Typically used for PET bottles, this method combines stretching and blowing to enhance the strength and clarity of the material. This process can either be in one-step or two-step configurations.
Applications Across Industries
The blow molding process is indispensable across various sectors, including:
- Food and Beverage: Most plastic bottles for soft drinks and water are produced using blow molding processes, ensuring consumer demands are met in terms of safety and sustainability.
- Pharmaceuticals: The medical industry benefits from blow molding in creating precise labels, containers, and other application-specific components.
- Automotive: Parts such as fuel tanks, fenders, and various interior components can be manufactured through blow molding, aiding in weight reduction and cost-saving.
- Consumer Goods: From toys to household items, blow molding serves to manufacture a wide range of products tailored to consumer needs.
Choosing a Reliable Blow Molding Machine Manufacturer
Selecting the right blow molding machine manufacturer involves careful consideration of several factors that can influence production efficiency and quality. Here are some vital aspects to keep in mind:
Key Factors to Consider
When evaluating potential blow molding machine providers, consider the following:
- Quality of Machines: Assess the material quality and engineering of the machines. Reliable manufacturers often provide robust machines built to last, with minimal downtime.
- Technological Advancements: Manufacturers should offer the latest technology features, including automation capabilities, process control, and energy efficiency to enhance productivity.
- Range of Options: Determine if the manufacturer provides various types of machines to meet the specific needs of your operation. For instance, consider if they offer both EBM and IBM machines.
Evaluating Manufacturer Credentials
It’s crucial to verify the manufacturer’s credentials to ensure you are choosing a reputable supplier. Consider reviewing the following:
- Industry Experience: Look for manufacturers with a significant track record in the blow molding industry. Companies like Uniloy and Wilmington Machinery are recognized for their longevity and innovation.
- Certifications: Reputable manufacturers often hold industry certifications that demonstrate compliance with quality standards (e.g., ISO certifications).
- Client Testimonials: Seek feedback from current users and case studies, which can provide insights into the manufacturer’s reliability and service quality.
Understanding Customer Support and Service
Robust customer support is vital in ensuring smooth operations. Important support aspects include:
- Training: The manufacturer should offer thorough training for your staff to ensure they can operate the blow molding machines efficiently.
- Maintenance and Repair: Inquire about the support structure for maintenance and repairs, including response times and availability of spare parts.
- Technical Support: Easy access to technical support can enhance the machine’s operational uptime, providing assistance when it’s needed the most.
Innovations in Blow Molding Technology
The blow molding industry continues to evolve with advancements in technology, driving increased efficiency and capability. Below are key innovations shaping the future of blow molding:
Advanced Machinery Features
Today’s blow molding machines come equipped with various advanced features to improve performance and productivity, including:
- Automation: Automation technologies enable machines to operate with minimal human intervention, increasing speed and consistency in production.
- Energy Efficiency: New machine designs often incorporate energy-saving components, contributing to lower operational costs and enhanced sustainability.
- Real-Time Monitoring: Features that allow real-time monitoring of production processes enable manufacturers to detect issues early and optimize their processes to reduce waste.
Integration with Industry 4.0
The rise of Industry 4.0 is influencing blow molding processes, with manufacturers increasingly integrating smart technology into their machinery. Key aspects include:
- Data Analytics: Collecting and analyzing data can help manufacturers optimize processes and predict maintenance needs.
- Interconnectivity: Machines that are part of a smart manufacturing system can communicate with each other and share data across networks, enhancing overall factory efficiency.
- Remote Control: Advanced machines allow for remote monitoring and control, enabling operators to manage processes from virtually anywhere.
Environmental Considerations
As sustainability becomes more critical across industries, blow molding technology is adapting by incorporating:
- Recyclable Materials: The use of eco-friendly materials and processes reduces environmental impact. Innovations in material science are paving the way to use more sustainable options in blow molding.
- Reduced Waste: Improvements in manufacturing processes are leading to less plastic waste generated during production, making operations more environmentally friendly.
- Energy Recovery Systems: Implementing systems that recover and reuse energy can significantly reduce the energy footprint of blow molding operations.
Cost Considerations for Blow Molding Machines
Investing in blow molding machines involves various costs that must be carefully managed to ensure profitability. Here are several financial aspects to consider:
Factors Affecting Pricing
The cost of blow molding machines can vary significantly based on several factors:
- Machine Type: The type of blow molding machine (EBM, IBM, or stretch blow molding) can dictate pricing variations.
- Production Capacity: Higher capacity machines tend to have higher price tags due to their increased complexity and capabilities.
- Customization: Specialized features and custom designs tailored to specific applications can further drive up costs.
Budgeting for Equipment Purchase
When budgeting for your blow molding equipment, consider the following steps:
- Initial Cost Estimates: Collect quotes from multiple manufacturers to understand the average pricing and avoid overpaying.
- Long-term Operational Costs: Consider factors like energy consumption, maintenance, training, and downtime, which can significantly affect budget long-term.
- Financing Options: Explore financing options, such as leasing or loans, to ease the initial financial burden.
Identifying Cost-effective Solutions
To ensure cost-effectiveness without compromising quality, consider:
- Used Equipment: Investigating reputable pre-owned blow molding machines can provide significant savings.
- Low-Cost Innovations: Manufacturers that offer innovative solutions that reduce production costs without sacrificing performance can be ideal partners.
- Partnerships: Establish long-term relationships with manufacturers, allowing for discounts on maintenance or upgrades.
Future Trends in Blow Molding
As the manufacturing landscape continues to evolve, various trends are set to shape the future of blow molding:
Emerging Market Demands
The demand for sustainable packaging solutions continues to rise, driven by consumer preferences and regulatory pressures. Manufacturers are responding by innovating their production methods and exploring alternative materials.
Technological Advancements to Watch
The industry is gearing towards:
- Bio-based Plastics: The use of bio-based plastics is gaining traction, with manufacturers exploring biodegradable options that cater to environmentally conscious consumers.
- Smart Manufacturing: Embracing smart manufacturing practices will allow for increased efficiency and lower production costs.
- Vertical Integration: More manufacturers are considering vertical integration of supply chains for greater control over raw materials and finished products.
Preparing for the Future of Manufacturing
To remain competitive, businesses should:
- Invest in R&D: Fostering innovation through research and development initiatives can help stay ahead of the curve.
- Flexibility: Implementing agile manufacturing practices allows manufacturers to pivot quickly in response to market changes.
- Employee Training: Continuous training programs ensure that employees are skilled in using emerging technologies and methodologies.