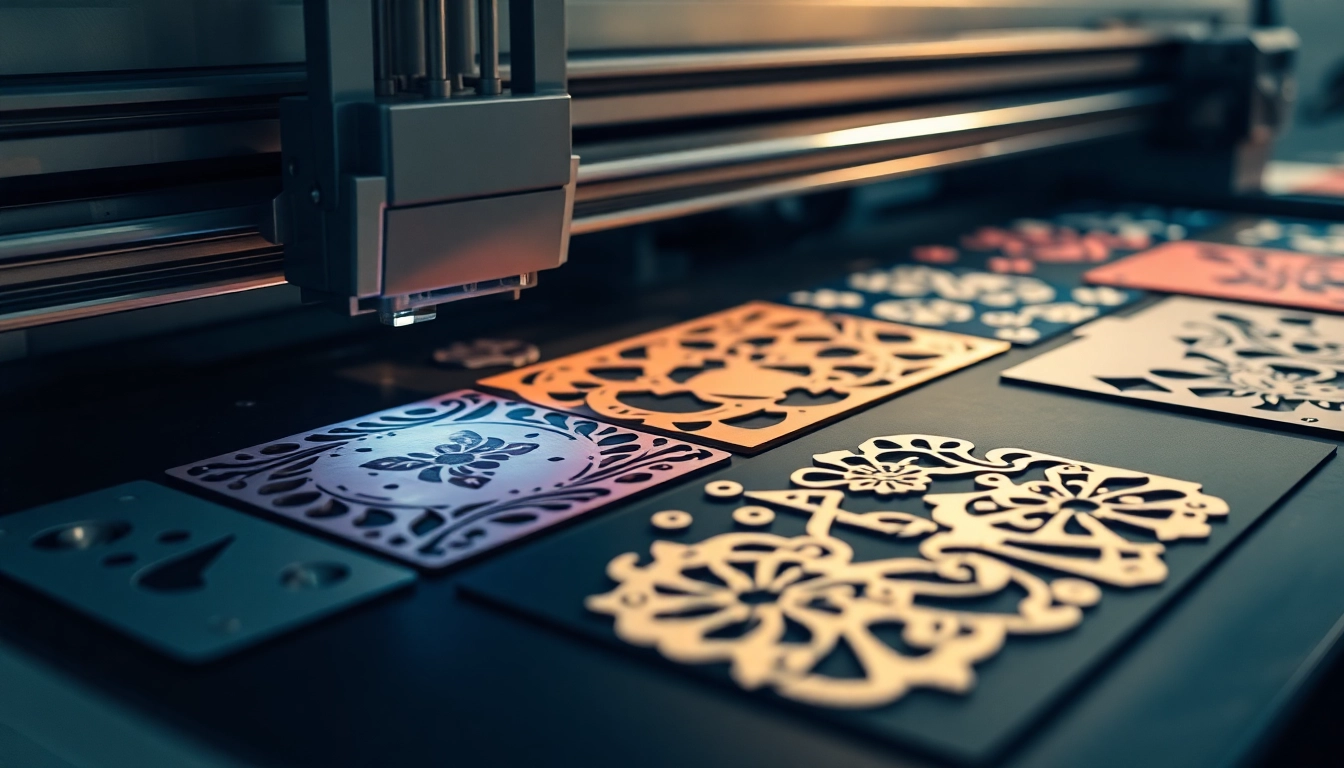
Understanding Precision Die Cutting
What is Precision Die Cutting?
Precision die cutting is a manufacturing process that utilizes specialized equipment to convert material into specific shapes and sizes through a mechanical cutting method. The process involves the use of a die, which is a specialized tool made from various metals that cut through the material with absolute accuracy, making it an essential technique in various industries such as automotive, medical, packaging, and electronics. The precision aspect refers to the ability to create consistent and exact dimensions for each component produced, which is vital in applications where tight tolerances are required. With technological advancements, precision die cutting has become more sophisticated, enabling manufacturers to cater to complex designs and a variety of materials.
Applications of Precision Die Cutting in Various Industries
The versatility of precision die cutting allows it to be widely used across multiple sectors. In the automotive industry, components such as gaskets, seals, and insulation parts are commonly produced through this method, ensuring they fit perfectly into larger assemblies. The medical field also benefits greatly from precision die cutting through the production of sterile packaging and medical device components, where contamination is a significant concern.
Packaging industries leverage precision die cutting to create custom boxes, labels, and inserts that enhance product presentation and protection. In electronics, precision die cuts are integral for circuit boards, insulators, and even packaging materials. Each application not only showcases the precision cutting capabilities but also highlights the importance of customization in meeting specific industry requirements.
Key Benefits of Using Precision Die Cutting Techniques
Employing precision die cutting techniques provides numerous benefits, including:
- High Accuracy: The precision in die cutting ensures that components fit perfectly and function as intended, reducing the need for rework and scrap.
- Cost-Effectiveness: While initial setup costs for dies may be higher, the efficiency and speed of production often lead to lower overall costs, especially for high-volume runs.
- Material Efficiency: Precision die cutting minimizes waste, enabling companies to maximize material usage while producing high-quality products.
- Versatility in Material Use: From paper and cardboard to plastics and metals, precision die cutting can handle a wide range of materials, making it adaptable to various production needs.
- Rapid Prototyping: Faster turnaround times during the prototyping phase help companies accelerate their product development cycles.
Types of Precision Die Cutting Methods
Flatbed Die Cutting: Overview and Applications
Flatbed die cutting involves a hydraulic flatbed press that applies pressure to cut material with precision. This method is particularly well-suited for thicker materials and cutting larger pieces with intricate shapes. It is widely used in the packaging industry for creating prototypes, samples, and volumes requiring detailed cuts.
Applications often include producing custom boxes, display stands, and signage where the strength and durability of the cut materials are essential. The technique can handle various materials, including paper, foam, and plastic, making it a popular choice for product packaging.
Rotary Die Cutting: Efficiency and Versatility
Rotary die cutting utilizes a rotating cylinder with blades around its circumference. As the cylinder turns, it cuts the material as it advances through the machine. This method is particularly efficient for high-volume production runs due to its speed and ability to produce continuous rolls of die-cut materials.
Industries such as food and beverage, consumer goods, and label printing benefit from rotary die cutting, allowing them to produce large quantities of consistent and precise parts. The method’s efficiency not only contributes to lower costs but also enhances production timelines significantly.
Laser Die Cutting: Precision and Customization
Laser die cutting harnesses the power of lasers to cut materials with exceptional precision. This method is particularly valuable for intricate designs and materials that may be challenging to cut using traditional methods. With laser cutting, manufacturers can achieve complex shapes without the need for expensive physical dies, making it an attractive option for low-volume production or prototyping.
The technology is widely applied in the textile, aerospace, and automotive industries, where it aids in producing parts with very tight tolerances and complex geometries. Additionally, laser die cutting allows for quick adjustments to designs, enabling faster implementation of new ideas and concepts.
Choosing the Right Precision Die Cutting Partner
Key Criteria for Selecting a Die Cutting Vendor
When selecting a die cutting partner, it’s essential to consider several factors to ensure high-quality results. Look for vendors with proven experience in your specific industry, as they will be more familiar with your unique requirements. Assess their technology and equipment, as modern machinery can greatly enhance accuracy and efficiency. Customer reviews and case studies can provide insights into their reliability and performance.
Additionally, consider their capacity for customization and flexibility in meeting deadlines, especially if your demands change frequently. Good communication and customer service are also paramount in fostering a productive partnership.
Factors Influencing Cost and Quality of Precision Die Cutting
The cost of precision die cutting can be influenced by various factors, including the type of die used (flatbed, rotary, or laser), the materials involved, and the complexity of the design. Higher material costs or intricate designs may lead to increased production expenses. However, the overall quality is paramount, as lower-quality dies can result in defects that could ultimately lead to higher costs through rework or waste.
Volume plays a critical role too; larger production runs typically reduce unit costs due to economies of scale. Establishing a clear understanding of your project requirements and discussing budgetary constraints with your die cutting partner can assist in finding the right balance between cost and quality.
How to Evaluate Die Cutting Service Performance
Evaluating the performance of your die cutting service involves measuring several key performance indicators (KPIs). Consider monitoring factors such as turnaround times, material waste rates, defect rates, and overall customer satisfaction. Regular feedback loops with your vendor can foster improvements and align production practices with your business objectives.
In addition, conducting regular audits of samples against specifications can ensure ongoing quality control. By remaining proactive in your evaluations, you can ensure that your die cutting processes consistently meet industry standards and your company’s unique requirements.
Design Considerations for Precision Die Cutting
Material Selection for Optimal Die Cutting
The choice of materials is critical in achieving optimal results in precision die cutting. Factors such as thickness, flexibility, and durability should be evaluated based on the application. Common materials include paper, cardboard, plastics, metals, and foams, each inviting different considerations in terms of die design and cutting methods.
It’s essential to understand how these materials will behave during the die cutting process, including their potential for deformation or wear. Working closely with your die cutting partner to understand the properties of your selected materials can lead to better design decisions and higher quality outputs.
Design Tips to Ensure Precision Die Cuts
To ensure your die cuts are precise and meet your specifications, consider the following design tips:
- Simplify Designs: Complex shapes can complicate the cutting process. Simplifying design can help in achieving cleaner cuts.
- Account for Tolerances: Be aware of the tolerances required for your components. For precision applications, tight tolerances are crucial, so ensure your designs take this into account.
- Use Break Lines: Incorporate break lines into designs to assist in the removal of products from the die without damaging cutting edges.
- Test Cuts: Conduct test cuts with the chosen material to ensure that the cuts meet quality standards before moving forward into full production.
Common Mistakes to Avoid in Die Cutting Design
Designing for die cutting includes navigating various potential pitfalls that can affect the outcome. Some common mistakes include:
- Ignoring Material Properties: Not taking into account how different materials behave during cutting can lead to costly errors.
- Avoiding Communication: Failing to discuss design specifications adequately with your cutting partner may lead to misunderstandings and issues in production.
- Overlooking Tolerances: Not considering tolerances can result in parts that are too tight or too loose, leading to functionality issues.
- Rushing the Design Process: Taking the time to refine and review designs thoroughly can prevent costly mistakes that may arise in production.
Future Trends in Precision Die Cutting
Emerging Technologies and Innovations in Die Cutting
The landscape of precision die cutting is continually evolving, with advancements in technology leading to new possibilities. Automation and robotics are becoming more prevalent, streamlining processes and reducing lead times. Additionally, software innovations allow for more complex design capabilities and simulations to test out designs before actual production.
Moreover, the rise of 3D printing technologies presents opportunities for hybrid manufacturing, where die cutting can be combined with 3D printing methods, enhancing customization limitations. Staying updated with these technological advancements is vital for manufacturers seeking competitive advantages.
Sustainability in Precision Die Cutting Processes
As sustainability becomes a core focus across industries, precision die cutting is not exempt. Rising awareness about environmental impacts is inducing manufacturers to explore greener processes, such as using recyclable materials or waste reduction techniques. Advancements in technology also enable companies to optimize production processes, resulting in fewer emissions and lower energy usage.
Incorporating sustainable practices not only aligns with global trends but also enhances brand reputation, appealing to increasingly eco-conscious consumers.
The Impact of Industry 4.0 on Precision Die Cutting Services
Industry 4.0 is transforming manufacturing, including precision die cutting. The implementation of IoT, big data, and AI is improving efficiencies and lean manufacturing practices. Predictive analytics allows manufacturers to forecast demand and adjust production accordingly, minimizing waste and improving inventory management.
By embracing Industry 4.0 technologies, die cutting service providers can enhance decision-making processes, streamline operations, and provide customers with real-time insights into production and delivery schedules.